Adapted from the published manuscirpt: Chatterjee, A., Chahare, N. R., Kondaiah, P., & Gundiah, N. (2021). Role of Fiber Orientations in the Mechanics of Bioinspired Fiber-Reinforced Elastomers. Soft Robotics, 8(6), 640-650..
Introduction
Soft-bodied animals, such as sea anemones, octopi, and caterpillars, possess unique capabilities in maintaining posture, navigating narrow spaces, and generating movement. These abilities are attributed to their hydrostatic skeleton and differentially arranged muscles. Soft robotic applications, like actuators and grippers, require materials that are soft, flexible, and capable of large stretches. Fiber-reinforced elastomeric (FRE) materials offer these properties, making them ideal candidates for various applications, including exoskeletons, soft grippers, and bioinspired robots. This study aims to understand the nonlinear force–displacement relationships in FRE materials and their links to fiber orientations.
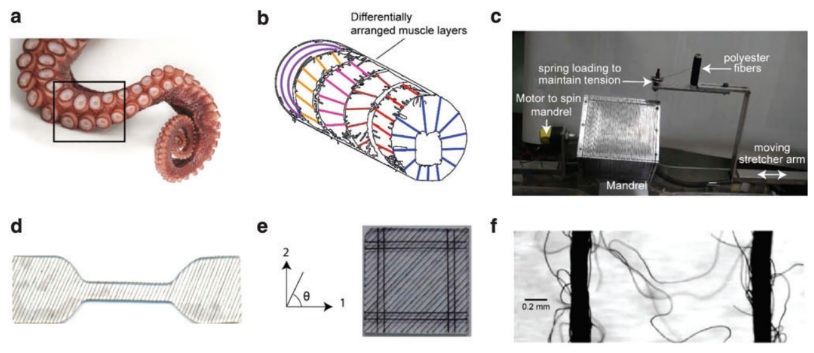
Methods
To achieve the study’s goals, FRE materials with varying fiber angles in transversely isotropic layouts were fabricated. Uniaxial and equibiaxial tests were performed to assess the constitutive model in FRE materials. Additionally, an inversion point in the deviatoric stress components was identified at the magic angle (54.7 degrees), which is associated with minimized shear strains.
Results
The experimental results provided valuable insights into the mechanics of fiber-reinforced elastomeric (FRE) materials. The uniaxial and equibiaxial tests conducted on FRE samples with varying fiber angles in transversely isotropic layouts demonstrated the individual contributions of fibers and the matrix to the overall mechanical behavior of the composite material. These contributions were quantified in terms of the strain energy density function (SEF), which is a fundamental concept in continuum mechanics that describes the relationship between stress and strain in hyperelastic materials.
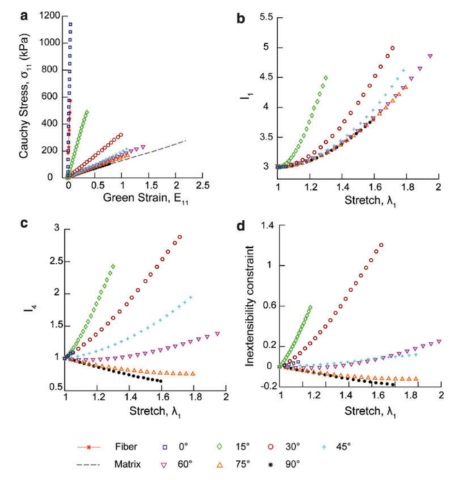
In hyperelastic materials, the constitutive relationship between stress and strain is nonlinear and can be expressed in terms of strain energy density. The strain energy density function encapsulates the material’s response to deformation and depends on the invariants of the right Cauchy-Green deformation tensor. In the case of FRE materials, the invariants of interest are I1 and I4, which are related to the stretches along the fiber direction and the stretches transverse to the fiber direction, respectively.
Based on the experimental results, a new form of the strain energy density function was proposed to accurately describe the stress–strain properties of FRE composites. This new form highlights the importance of including a coupling term that links the invariants I1 and I4. This coupling term accounts for the interaction between fibers and the matrix, which is crucial for capturing the nonlinear, anisotropic, and large deformations exhibited by FRE materials under various loading conditions.
Furthermore, the experimental results revealed an inversion in the deviatoric components of stress at fiber orientations corresponding to the magic angle (54.7 degrees). The magic angle is a well-known concept in the study of fiber-reinforced materials, as it results in a maximum enclosed cylindrical volume and minimal shear strains. This observation confirms the significance of fiber orientations in determining the overall mechanical behavior of FRE materials.
In conclusion, the comprehensive experimental results presented in this study offer a deeper understanding of the nonlinear mechanics of FRE materials, specifically focusing on the role of fiber orientations and the interactions between fibers and the matrix. The new constitutive model derived from these results can be used to further investigate the behavior of FRE materials in various applications, including soft robotics and biomechanics.
Conclusion
This study presents a novel constitutive model for FRE materials, which can be implemented in numerical schemes to study the effects of complex loading and boundary value conditions for flexible composite FRE materials. The data provided offer a robust method for testing analytical models for FRE materials with potential applications in biomechanics and soft robotics. These findings represent a crucial step toward investigating the mechanics of active elastomers and electrically actuated fibers in matrices that can mimic muscular hydrostatic skeletons in engineering applications.